VCRP™ for Hospital Supply Management
Vecco’s Hospital Supply Management (HSM) Sollution is a demand driven inventory visibility and planning and solution for Hospital/Provider Networks’ med/surg, drug and tech inventories. It ties together real-time data across entire networks, their many distributors, direct suppliers and even the ultimate OEMs.
HSM enables network wide visibility, planning and management of all hospital and clinical inventory investments whether currently recorded on financial records or currently expensed, but unused in hospital facilities. It detects potential supply issues and helps supply chain professionals to correct those issues that could cause unmet patient needs, excess inventories and material expiry losses. It generates valuable material demand and usage information by hospital business unit, separating out temporary inventory fluctuations and expiry losses from true material usage cost by department /unit. Unit Managers can gain true cost visibility.
Vecco is a leader in SAAS multi-tier healthcare supply chain planning / management solutions.
“Inventory improvement” in the health care world is all about ensuring patients and caregivers have the materials they need, when and where needed, but also at costs that are healthy for the provider itself. Drug, device and med-surg inventory management is one of the toughest challenges providers and provider networks face today. Materials represent up to 25% of network total operating costs, and markets/payers are pressuring all networks for continuous materials cost reductions.
Literally dozens of hardware, software and consulting companies have promised to deliver improvements, if hospitals only would make investments in new hardware, scanners, caregiver staff re-training, outsourcing supply chain management to 3rd parties, etc, but none of these yield game changing results to date, as they each optimize only one element of the problem, not the total picture.
Leading analysts believe Vecco’s new and radically cost effective SAAS hospital supply management solution has the potential to revolutionize provider network materials management.
HSM can easily be integrated with all existing provider network ERP and HER software and any existing cabinet / scanner solutions to dramatically enhance the accuracy of planning and fulfillment processes and to ensure that constraints and shortages are addressed before patient requirements are missed. The solution cuts the time caregivers spend on expediting and can reduce procedure cancellations due to device or material shortages.
Providers struggle with opaque and inefficient materials distribution. They are challenged with large, yet “invisible” facility inventories typically managed manually by PAR systems and roving staff armed with scanners and clipboards. In many cases, facility inventories are 8 to 10x the inventories held in a network’s distribution center, yet only the DC inventories are on any financial record. Caregivers frequently experience shortages as they attempt to react to unpredictable patient requirements and last minute demand / schedule changes. Experts estimate 10 to 20% of most nursing staff’s time is wasted in this manner, depending upon their specialty. Provider’s Operational Unit mangers also lack true, timely material cost information to use to optimize provider efficiency.
Further complications include evolving regulatory traceability requirements, managing consignments, dealing with effectivity and expiration dates, planning complex kitting requirements and managing reusable tools. Often time, items inadvertently get “lost in the shuffle” and don’t find their way back on to “official“ inventory records. This is a significant financial issue, and now, with regulatory traceability laws, is a compliance risk as well. These large facility inventories tie up significant cash resources, yet still fail to satisfy patient requirements without manual expediting between 2 and 5% of all cases. Too often, the correct device or package/dose is not available in a care location at a specific moment in time. To improve patient outcomes, even more costly inventory is added to the facility, too much of which then expires without meaningful use.
Most hospital supply chains are “powered” by a multiplicity of disparate IT & manual systems. Process execution can be highly fragmented. Until now there has been no platform well suited to solve the facility based inventory challenge without costly customization or resort to expensive automated inventory cabinets or dispensing systems.
Vecco works with all ERPs and HRMs, Scheduling systems, Warehouse Management systems, GHX, Pharmacy and vendor/distributor systems. We work with all common provider inventory tools, including cabinets, dispensing systems, fixed and mobile barcode scanners, and smartphone apps. We support consigned inventory of all kinds.
We understand that most of your materials in your facilities are not recorded in any financial or inventory system today. We take your existing data and synthesize records for every one of your stockrooms or cabinet systems or pharmacies in our solution. We then link these to your material replenishment systems and financial systems.
Our SAAS solution delivers multi-site, multi-partner inventory visibility, planning and management to providers. We work with your many existing ERPs, EHRs, inventory tools, scanners, manual processes, etc. We synthesize network wide and site / business unit / caregiver unit specific inventory and usage data in real time. we enable you to manage facility inventory even when it is not currently in one of your existing systems of record.
We enable real time links to your distribution, med-tech, pharma and other suppliers and data exchanges such as GHX to extend your visibility upstream into their and their OEM’s networks. We give you visibility over today and tomorrow’s issues. We enable your supply chain teams to make sound choices that optimize patient service at affordable cost, reducing shortages & expiry losses, reducing caregiver time spent on expediting and especially, affordably avoiding patient care delays.
Unit managers can review their actual costs by budget period, and see usage separate from expiry losses. This may be the first time your unit managers can begin to seriously link material choices and options to unit financial results in a rigorous manner.
New computers, scanners, cabinets or caregiver staff retraining are NOT required. We never require an organization wide “Big-Bang” project. We solve inventory problems in a single unit or category, or all inventories across a nationwide network. You prove value and realize improved fill rates at lower cost in critical areas one at a time, in priority sequence, paying for each phase with savings from the prior phase.
Enable Higher Patient Fill Rates with Lower Costs, Higher Caregiver Productivity and Improved Profitability
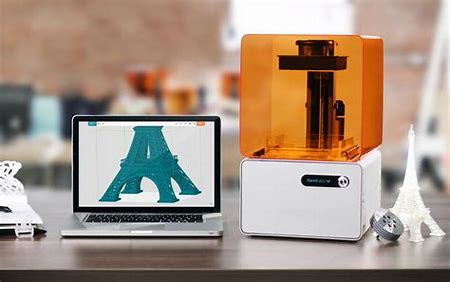
Formlabs Leverages Vecco to Manage Global Demand, Supply, and Inventory Operations
Leading 3D printer manufacturing company deploys next generation supply chain management system to orchestrate supply and demand across their rapidly expanding global supply chain. MALVERN, PA. Vecco International, provider of an advanced end-to-end cloud-based...